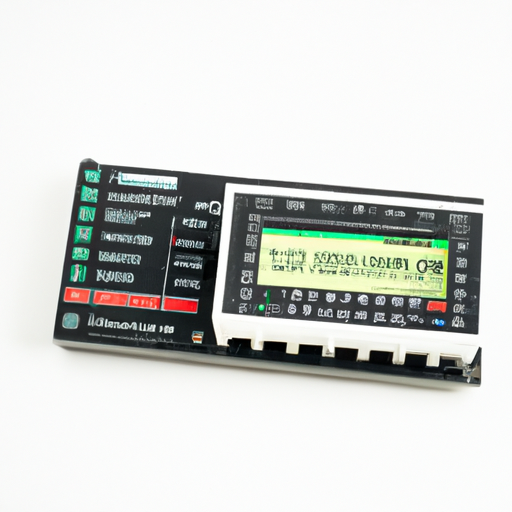
Overview of Programmable Timers and OscillatorsProgrammable timers and oscillators are critical components in modern electronic systems, enabling precise control over timing and frequency generation. While the MM74HC240N is primarily a hex buffer/driver, understanding the broader context of programmable timers and oscillators can provide insights into their functionalities and applications.
Core Functional Technology 1. Programmable Timers
- **Definition**: Programmable timers are integrated circuits designed to generate specific time delays or intervals, allowing for flexible timing control in various applications.
- **Key Features**:
- **Adjustable Time Intervals**: Users can set the duration for which the timer operates, making it adaptable to different needs.
- **Multiple Modes of Operation**: Timers can function in various modes, such as one-shot (single event) or periodic (repeating events).
- **Microcontroller Integration**: Programmable timers can easily interface with microcontrollers, allowing for straightforward programming and control.
- **Low Power Consumption**: Many programmable timers are designed for efficiency, making them suitable for battery-powered devices. 2. Oscillators
- **Definition**: Oscillators are circuits that produce a continuous periodic signal, often used for clock generation in digital systems. Programmable oscillators allow for frequency adjustments based on specific application requirements.
- **Key Features**:
- **Frequency Stability and Accuracy**: High-quality oscillators maintain consistent frequency output, which is crucial for reliable system performance.
- **Programmable Frequency Output**: Users can adjust the output frequency to meet the demands of various applications.
- **Waveform Generation**: Programmable oscillators can generate different types of waveforms, such as square, sine, or triangular waves.
- **Integration with PLL**: Phase-Locked Loops (PLLs) can be used with oscillators for advanced frequency synthesis and stability. Application Development Cases 1. Microcontroller-Based Timing Applications
- **Example**: In embedded systems, programmable timers are essential for scheduling tasks. For instance, a microcontroller can be programmed to activate a relay every hour, controlling lighting in smart homes or managing energy consumption. 2. Frequency Generation in Communication Systems
- **Example**: Programmable oscillators are crucial in RF communication systems for generating carrier frequencies. A programmable oscillator can dynamically adjust the frequency in a transceiver, optimizing communication channels based on real-time conditions. 3. Industrial Automation
- **Example**: Programmable timers are used to control machinery operations in industrial settings. For example, a timer can delay the start of a conveyor belt until all safety checks are confirmed, enhancing operational safety. 4. Consumer Electronics
- **Example**: In appliances like microwaves and washing machines, programmable timers allow users to set specific operation times, improving convenience and user experience. Timers can manage cooking cycles or washing durations effectively. 5. Automotive Applications
- **Example**: In automotive systems, programmable timers are utilized for functions such as turn signal timing and automatic headlight control. Precise timing is essential for safety features and overall vehicle performance. 6. Medical Devices
- **Example**: In medical applications, programmable timers are critical for dosage administration in infusion pumps, ensuring that medication is delivered at precise intervals, which is vital for patient safety and treatment efficacy. ConclusionProgrammable timers and oscillators play a pivotal role in enhancing the functionality and efficiency of electronic systems across various industries. Their ability to provide precise timing and frequency generation makes them invaluable in applications ranging from consumer electronics to industrial automation and medical devices. While the MM74HC240N serves as a buffer/driver, it can complement these technologies by ensuring signal integrity and driving outputs effectively in timing and frequency generation applications. Understanding the core functionalities and real-world applications of programmable timers and oscillators can empower engineers and developers to leverage these technologies in innovative ways.
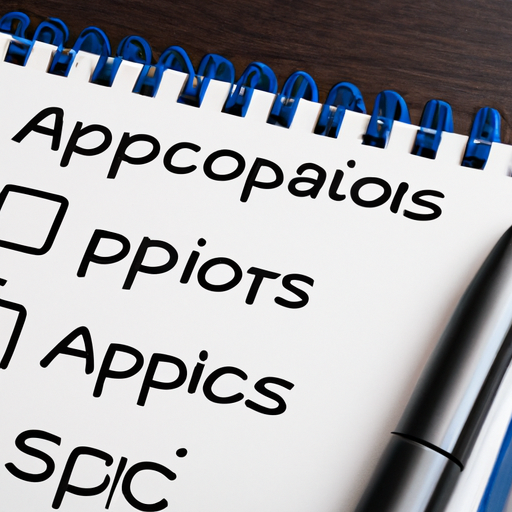
Application Development in Delay Lines for CFR-50JB-52-11R: Key Technologies and Success StoriesDelay lines, such as the CFR-50JB-52-11R, play a pivotal role in various high-tech applications, particularly in telecommunications, signal processing, and radar systems. While specific details about the CFR-50JB-52-11R model may not be available, we can explore the broader context of delay line technologies and their successful implementations.
Key Technologies in Delay Lines1. Digital Delay Lines2. Analog Delay Lines3. Fiber Optic Delay Lines4. Acoustic Delay Lines5. Integrated Circuit Delay Lines1. Telecommunications2. Audio Processing3. Radar Systems4. Fiber Optic Networks5. Consumer Electronics Success Stories ConclusionDelay lines, including models like the CFR-50JB-52-11R, are essential components in a wide array of modern technologies. Their development is continuously evolving, driven by advancements in digital signal processing, materials science, and integrated circuit design. The success stories across various industries underscore the critical role of delay lines in enhancing performance, reliability, and user experience. As technology progresses, we can anticipate further innovations in delay line applications, particularly in emerging fields such as 5G, IoT, and autonomous systems, paving the way for new possibilities in communication and signal processing.
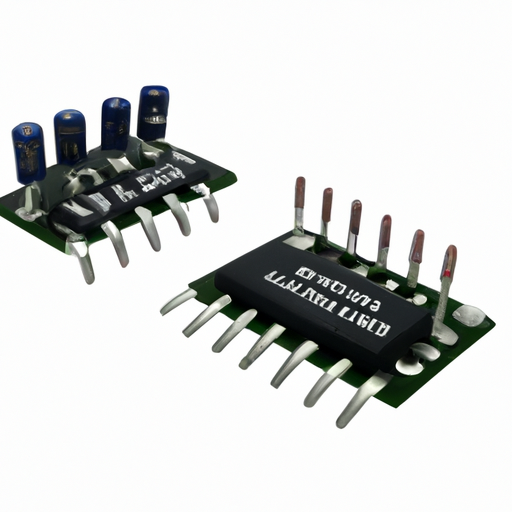
Certainly! Here’s a more detailed exploration of instrumentation amplifiers, operational amplifiers (op-amps), and buffer amplifiers, focusing on their core functional technologies and application development cases.
Instrumentation AmplifiersHigh Input Impedance: This characteristic allows instrumentation amplifiers to interface with high-impedance sources without drawing significant current, thus preserving the integrity of the signal.High Input Impedance: This characteristic allows instrumentation amplifiers to interface with high-impedance sources without drawing significant current, thus preserving the integrity of the signal.Differential Amplification: By amplifying the difference between two input signals while rejecting common-mode noise, instrumentation amplifiers are particularly effective in environments with electrical interference.Differential Amplification: By amplifying the difference between two input signals while rejecting common-mode noise, instrumentation amplifiers are particularly effective in environments with electrical interference.Adjustable Gain: The gain can be set using external resistors, providing flexibility for various applications. This is often achieved through a three-op-amp configuration.Adjustable Gain: The gain can be set using external resistors, providing flexibility for various applications. This is often achieved through a three-op-amp configuration.Versatility in Configuration: Op-amps can be configured in numerous ways (inverting, non-inverting, integrator, differentiator, etc.), allowing them to perform a wide array of functions.Versatility in Configuration: Op-amps can be configured in numerous ways (inverting, non-inverting, integrator, differentiator, etc.), allowing them to perform a wide array of functions.High Open-Loop Gain: This allows for precise control over the output through feedback mechanisms, enabling applications in linear and nonlinear systems.High Open-Loop Gain: This allows for precise control over the output through feedback mechanisms, enabling applications in linear and nonlinear systems.Low Noise and Offset Voltage: Many modern op-amps are designed to minimize noise and offset voltage, making them suitable for precision applications.Low Noise and Offset Voltage: Many modern op-amps are designed to minimize noise and offset voltage, making them suitable for precision applications.Unity Gain Configuration: Buffer amplifiers provide a gain of one, allowing them to transmit signals without amplification, which is crucial for maintaining signal integrity.Unity Gain Configuration: Buffer amplifiers provide a gain of one, allowing them to transmit signals without amplification, which is crucial for maintaining signal integrity.High Input and Low Output Impedance: This characteristic allows buffer amplifiers to isolate different circuit stages, preventing loading effects that could distort the signal.High Input and Low Output Impedance: This characteristic allows buffer amplifiers to isolate different circuit stages, preventing loading effects that could distort the signal.Signal Isolation: Buffers are used to decouple stages in a circuit, ensuring that the performance of one stage does not adversely affect another.Signal Isolation: Buffers are used to decouple stages in a circuit, ensuring that the performance of one stage does not adversely affect another.1. Medical Devices:2. Industrial Sensors:3. Data Acquisition Systems:1. Signal Conditioning:2. Active Filters:3. Analog Computation:1. Impedance Matching:2. Signal Isolation:3. Voltage Followers: Operational Amplifiers (Op-Amps) Buffer Amplifiers ConclusionInstrumentation amplifiers, operational amplifiers, and buffer amplifiers are foundational components in analog electronics, each serving unique roles in signal processing and conditioning. Their diverse applications span across medical devices, industrial automation, consumer electronics, and data acquisition systems. Understanding their core technologies and application cases enables engineers to design more effective and efficient electronic systems, ensuring high performance and reliability in various applications.
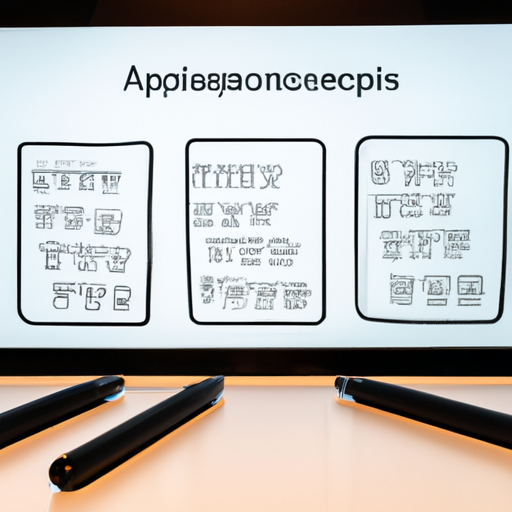
Application Development in Specialized ICs for IRF510: Key Technologies and Success StoriesThe IRF510 is a widely recognized N-channel MOSFET that plays a crucial role in various electronic applications, including power amplifiers, switching power supplies, and motor control systems. The development of specialized integrated circuits (ICs) tailored for the IRF510 has led to significant advancements in performance, efficiency, and reliability. Below, we explore key technologies and notable success stories associated with the IRF510.
Key Technologies1. Power Management ICs (PMICs)2. Driver ICs3. Thermal Management Solutions4. Digital Control Systems5. Integrated Protection Circuits1. RF Amplifiers2. Switching Power Supplies3. Motor Control Applications4. LED Drivers5. Renewable Energy Systems Success Stories ConclusionThe IRF510 continues to be a versatile and essential component in a wide range of applications. The development of specialized ICs has significantly enhanced its performance and reliability, enabling engineers to create innovative solutions across multiple industries. By leveraging key technologies such as power management, driver circuits, and digital control systems, the potential for new applications and improvements in existing designs is vast. As technology evolves, the IRF510's role in modern electronics is likely to expand, further solidifying its importance in the field.
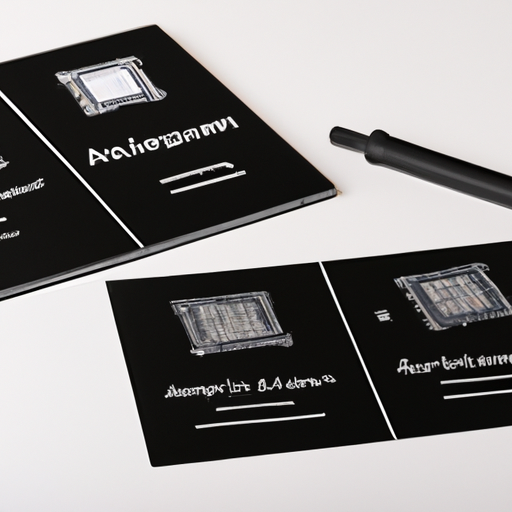
Application Development in Laser Drivers for MM74HC241N: Key Technologies and Success StoriesThe MM74HC241N is a high-speed CMOS octal buffer/driver with 3-state outputs, commonly utilized in digital circuits for driving signals. While it is not a dedicated laser driver, it plays a crucial role in systems that incorporate laser drivers, particularly in applications such as optical communication, laser printing, and various photonics technologies. Below is an overview of key technologies and success stories related to application development in laser drivers that may involve components like the MM74HC241N.
Key Technologies1. High-Speed Digital Logic:2. Laser Diode Drivers:3. Modulation Techniques:4. Temperature Control:5. Feedback Control Systems:6. Optical Communication Systems:1. Optical Fiber Communication:2. Laser Printing Technology:3. Medical Laser Systems:4. Industrial Laser Applications:5. Consumer Electronics: Success Stories ConclusionWhile the MM74HC241N itself is not a laser driver, its role as a high-speed buffer/driver in digital circuits is essential in various applications involving laser technology. The integration of such components in laser driver circuits has led to significant advancements in optical communication, printing technology, medical devices, and industrial applications. As technology continues to evolve, the demand for efficient and reliable laser drivers will likely lead to further innovations and success stories in this field, highlighting the importance of components like the MM74HC241N in modern electronic systems.
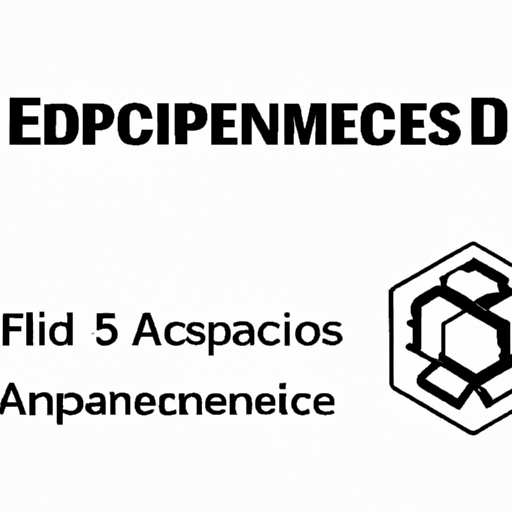
Application Development in TRIACs for ECS-F1VE685K: Key Technologies and Success StoriesThe ECS-F1VE685K TRIAC is a versatile semiconductor device that plays a significant role in controlling power in AC circuits. Its applications span across various domains, including lighting, motor control, heating systems, and consumer electronics. Below, we delve into the key technologies that enhance the functionality of TRIACs and highlight notable success stories that demonstrate their impact.
Key Technologies1. Phase Control2. Zero-Cross Detection3. Opto-Isolation4. Microcontroller Integration5. Thermal Management1. Smart Lighting Systems2. Industrial Motor Control3. Home Automation4. Heating Systems5. Consumer Electronics Success Stories ConclusionThe ECS-F1VE685K TRIAC exemplifies the critical role of TRIACs in modern electronic applications, particularly in power control and automation. By leveraging key technologies such as phase control, zero-cross detection, and microcontroller integration, developers can create innovative solutions that enhance efficiency, safety, and user experience. The success stories in smart lighting, industrial motor control, home automation, heating systems, and consumer electronics underscore the versatility and effectiveness of TRIACs across various sectors, paving the way for future advancements in power management and control technologies.
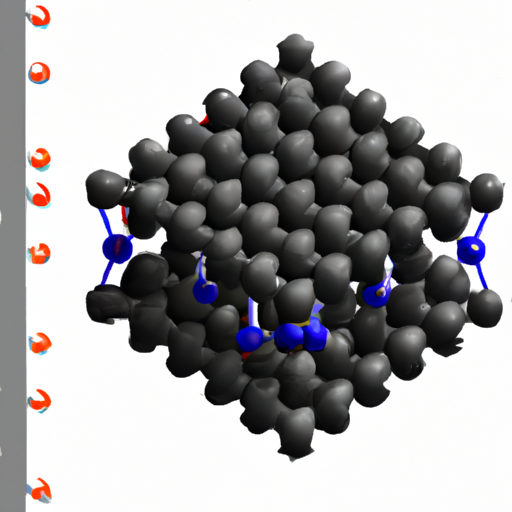
Overview of Bipolar Transistor Arrays, Pre-Biased: ECQ-P1H153GZBipolar Transistor Arrays, such as the ECQ-P1H153GZ, are integral components in modern electronic systems, providing essential functionalities like load driving, signal switching, and current amplification. This overview highlights the core functional technology, relevant articles, and application development cases that showcase the effectiveness of pre-biased bipolar transistor arrays.
Core Functional Technology1. Bipolar Junction Transistor (BJT) Fundamentals2. Array Configuration3. Pre-Biasing Advantages1. Technical Datasheets2. Application Notes3. Research Publications1. LED Drivers2. Motor Control3. Signal Switching4. Audio Amplification5. Power Management Articles and Resources Application Development Cases ConclusionBipolar Transistor Arrays, such as the ECQ-P1H153GZ, are crucial components in contemporary electronics, offering enhanced performance through pre-biased configurations. Their versatility across applications—from LED drivers to motor control and audio amplification—demonstrates their significance in meeting the demands of modern electronic systems. By leveraging the core technologies and insights from relevant articles and application cases, engineers can effectively design and implement innovative circuits that optimize performance and efficiency.
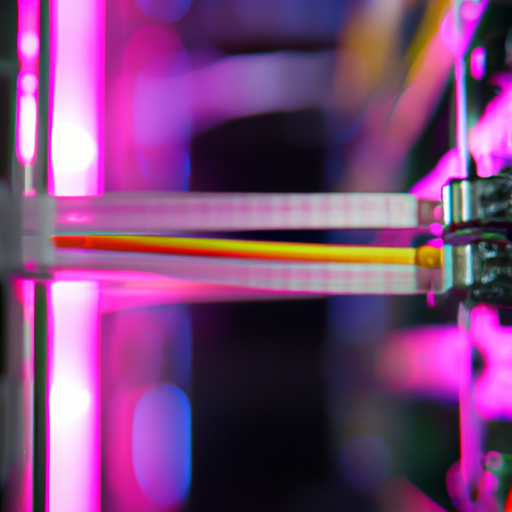
Application Development in Single, Pre-Biased Bipolar Transistors for ECQ-P1H333GZ: Key Technologies and Success StoriesSingle, pre-biased bipolar transistors, such as the ECQ-P1H333GZ, are specialized components that play a crucial role in various electronic applications. Their design allows for efficient operation under specific conditions, making them ideal for consumer electronics, automotive systems, and industrial equipment. Below is an overview of the key technologies and success stories associated with their application development.
Key Technologies1. Pre-Biasing Techniques2. Thermal Management3. Integrated Circuit Design4. Simulation and Modeling5. Packaging Innovations1. Consumer Electronics2. Automotive Applications3. Industrial Automation4. Telecommunications5. Renewable Energy Systems Success Stories ConclusionThe application development of single, pre-biased bipolar transistors like the ECQ-P1H333GZ exemplifies the convergence of advanced technology and practical engineering solutions. By leveraging innovations in design, thermal management, and packaging, these transistors have achieved success across various industries, driving improvements in performance, efficiency, and reliability. As technology continues to advance, the role of these components is expected to expand, paving the way for new applications and enhanced capabilities in the future.
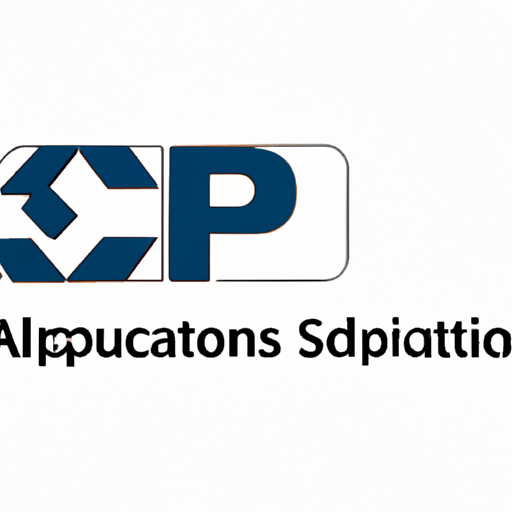
Application Development in SCRs - Modules for CFR-25JB-52-10R: Key Technologies and Success StoriesThe development of applications using Silicon Controlled Rectifiers (SCRs), particularly in modules like CFR-25JB-52-10R, involves a combination of advanced technologies and innovative methodologies. SCRs are pivotal in power electronics, especially for applications requiring high voltage and current control. Below, we explore the key technologies and notable success stories that illustrate the impact of SCRs in various sectors.
Key Technologies1. Power Electronics Design2. Control Systems3. Simulation Tools4. Protection Circuits5. Communication Protocols1. Industrial Motor Control2. Power Supply Systems3. Renewable Energy Systems4. HVDC Transmission5. Home Automation Success Stories ConclusionThe application development of SCRs, especially in modules like CFR-25JB-52-10R, harnesses cutting-edge technologies in power electronics, control systems, and communication. The success stories across various industries underscore the versatility and effectiveness of SCRs in enhancing energy efficiency, reliability, and performance. As technology continues to advance, the integration of SCRs with emerging technologies such as IoT and artificial intelligence is expected to drive further innovation, leading to more sophisticated and efficient solutions in the future.
Core Functional Technologies of IGBT Arrays1. High Efficiency and Low Switching Losses2. Thermal Management3. Integrated Gate Drivers4. Robust Protection Features5. Modular Design1. Renewable Energy Inverters2. Electric Vehicle (EV) Drives3. Industrial Motor Drives4. HVAC Systems5. Power Supply Units6. Welding Equipment Application Development Cases ConclusionThe 2474-26L IGBT array represents significant advancements in IGBT technology, offering high efficiency, robust protection features, and versatility across a wide range of applications. Its integration into renewable energy systems, electric vehicles, industrial drives, HVAC systems, power supplies, and welding equipment underscores the effectiveness of IGBT arrays in modern power electronics. As technology continues to evolve, IGBT arrays will remain pivotal in driving more efficient and sustainable energy solutions, contributing to the global transition towards cleaner energy sources.
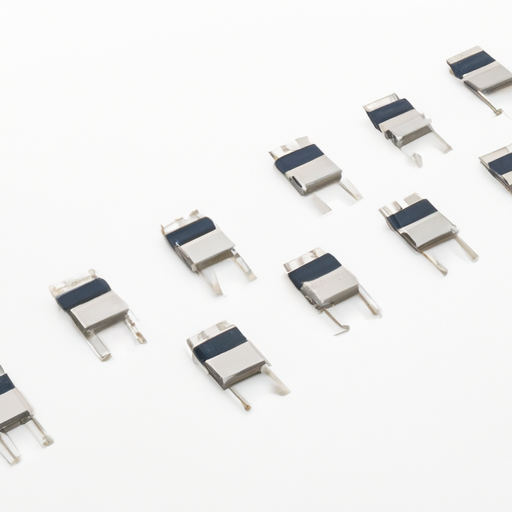
Overview of FET and MOSFET Arrays: Core Functional Technology and ApplicationsFET (Field Effect Transistor) and MOSFET (Metal-Oxide-Semiconductor Field-Effect Transistor) arrays are pivotal in modern electronics, particularly in applications that demand high efficiency, low power consumption, and compact designs. While the specific part number CFR-25JB-52-100K may refer to a particular FET or MOSFET array, the following overview provides insights into the core functional technology and various application development cases for these components.
Core Functional Technology1. Basic Operation2. Types of FETs3. Array Configuration4. Key Characteristics1. Power Management2. Motor Control3. Signal Switching4. LED Drivers5. Telecommunications6. Automotive Applications Application Development Cases ConclusionFET and MOSFET arrays are essential components in a wide array of electronic applications, providing efficient switching, amplification, and control. Their versatility and performance characteristics make them suitable for modern electronic designs, ranging from consumer electronics to industrial automation and automotive systems. As technology continues to evolve, advancements in materials and designs will further enhance the capabilities of FET and MOSFET arrays, paving the way for innovative applications. For specific part numbers like CFR-25JB-52-100K, it is advisable to consult the manufacturer's datasheet for detailed specifications, application notes, and design guidelines tailored to that component. This will provide insights into its unique features and optimal use cases.